Cattle Bells
Like any other craft, the craft of copper coated bells evolved from the need of the time and region. In earlier times, before the division of India and Pakistan, there used to be constant movement of people between these regions. Live-stock was a major occupation in Kachchh. The Lohar community from Sindh, (now in Pakistan) saw the potential for their craft and brought the craft to the land of Kachchh.
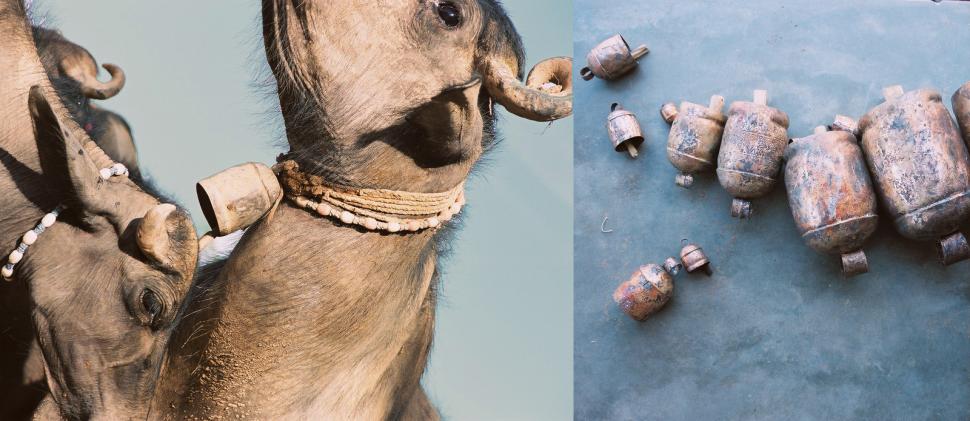
Buffalo from Banni wearing a metal bell
Ancestors of copper bell makers sold their products to the local communities. Maldharis Bharvads and Rabaris (pastoral communities) were their major clientele and shared a very close relationship with the bell artisans. The Bharvads and Rabaris would sit with the bell makers describing the sound that their cattle recognize. The bell makers set the sound and tone till his client felt convinced of the sound. The bells come at a very high price and carry a life-time warranty. If there is any change in sound or the shining fades, then the copper bell artisans refurbish it free of cost. Almost all the live-stock was adorned with their bells thus providing a very good market.
Old timers often refer to the bells by their original names such as chota paila, paila dingla, do dingla rather than the sizes. These names are the local currency equivalents for which bells could be bought at the time.
New Takes on the Craft
As the metal used in these bells is mostly waste tin and iron, this creative industry is a good example of recycling with aesthetics and utility. A local economy for the bells still exists unlike in the other crafts as these bells are used for identifying cattle by the cattle rearing communities of the region.
Most of the copper bell artisans desire their next generation to take up the craft as an occupation. The reinforcing factors were it was the family trend, and also the business being profitable and in demand. The artisans are also of the view-point that, with fewer job opportunities and the volatile nature of it, the craft skills ensure that one need not sleep hungry.
Today, the bells are referred by their sizes that range from 0-13, with size 0 being the smallest and size 13 being the largest. Natural resources used for copper bell making are mud, wood of ‘Prosophis Julifera’ and water. Mud is easily available at Zura village; and water is not required in much quantum; bell makers have reported scarcity of good quality wood as the charcoal makers destroy large portions of ‘Prosopis Julifera’.
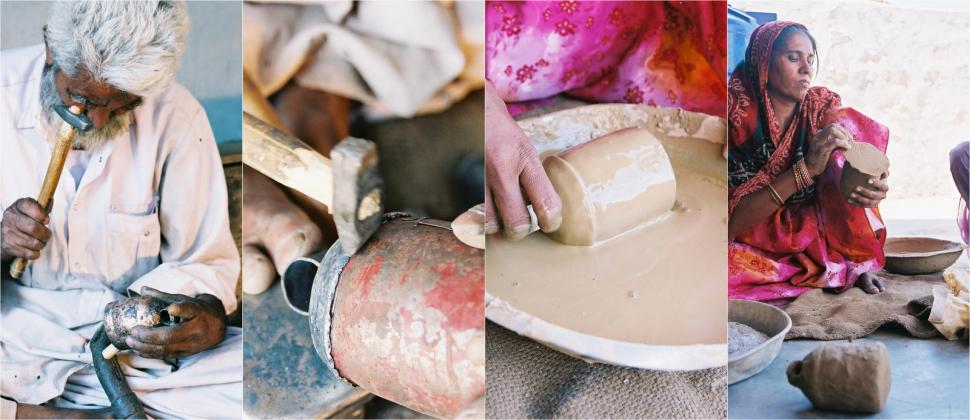
Process of bell making
The metal bell artisans have been sustained since the last 40 years through a business relationship with a major buyer from the US who buys these bells as Christmas merchandise. The sector is now at a crossroads where an up gradation in techniques, product diversification and better returns are becoming a need for the artisans. The younger generation needs to see a future in order to continue their fathers’ occupations.
Tomorrow’s Bell Chime
Findings show that the profit margins are very low in this sector. With associated artisans controlling 25% of the craft market share, Khamir has enabled the artisans to demand fair wages from buyers. Through a partnership with IICD Jaipur, Khamir worked with bell artisans to improve metallurgy and product diversity. A range of new metal finishes and products emerged, which were consumer tested at national fairs and in the Khamir outlet.
As the popularity of the craft grows, more protection for artisans in this risky craft must be put in place. To this end, Khamir helped implement safety measures for village workplaces including distribution of safety kits and helped artisans get health insurance. Using indigenous local skills and resources Khamir built a prototype of a closed firing kiln. It has now been tested successfully and is being adopted by artisans’ in their work places. Khamir was supported in these activities by SETU – The Bridge to Artisans, who has been a committed buyer of this craft. Technical guidance was given by the Hazards Center, Delhi, Ramzubhai Kumbhar ( a local potter ) and Prithvi Singh Deo, a ceramic artist.